Challenges
★ Full assembly parts delivery, complex color and texture solution
★ Leather covered surface
★ Details in strict accordance with the 3D files
★ Assembly of electrical fit parts
★ Functional test
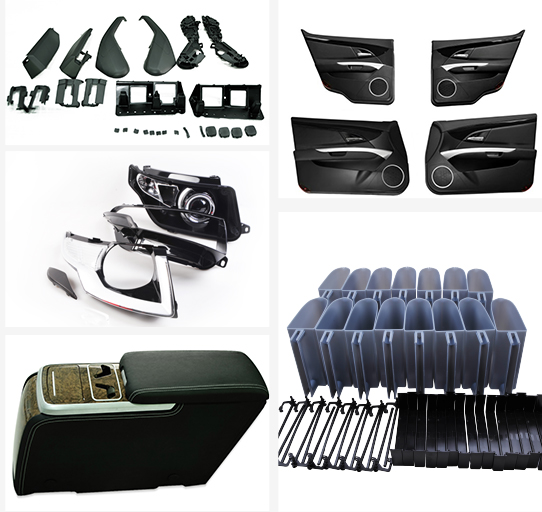
•
•
•
RPWORLD Solutions
Flexible production process for different function and quantity, including 3D printing, CNC, vacuum casting, RIM, injection molding, sheet metal fabrication.
High capability in surface treatment, including plating, anodizing, water transfer printing, painting, etc.
Full solution to requirements on engineering analyzing, material, technics and surface treatment.