Wussten Sie, dass das Spritzgießen die Medizintechnikbranche verändert? Mit diesem fortschrittlichen Verfahren können Konstrukteure qualitativ hochwertige und kosteneffiziente Produkte herstellen, die von gewöhnlichen medizinischen Artikeln bis hin zu stark regulierten Geräten reichen. Während die Produkte die verschiedenen Entwicklungsstadien durchlaufen - vom ersten Prototyp bis zur Serienproduktion - müssen sie stets die strengen Normen für Konformität, Sicherheit und Funktionalität erfüllen. Auf diese Weise wird sichergestellt, dass jedes medizinische Gerät in jeder Phase den wichtigen Anforderungen der Branche entspricht.
Wenn Sie den nächsten Schritt im medizinischen Spritzguss in Erwägung ziehen, finden Sie in diesem Artikel einen Leitfaden mit 4 wichtigen Überlegungen zum medizinischen Spritzguss, vom Verständnis der Geräteklassifizierungen und Vorschriften bis hin zur Auswahl geeigneter Materialien und der Vorbereitung Ihres Designs.
Wichtige Überlegungen zum medizinischen Spritzgießen
1. Einhaltung gesetzlicher Vorschriften: Entsprechende Normen einhalten
Die Richtlinien der Food and Drug Administration (FDA) in den USA schreiben eine strenge Verfolgung und Dokumentation in jeder Produktionsphase vor, um die Rückverfolgbarkeit jeder Komponente zu gewährleisten. In der EU hingegen legen die Normen der Medical Device Regulation (MDR) den Schwerpunkt auf eine konsistente Produktsicherheit über den gesamten Lebenszyklus des Geräts und zwingen die Hersteller zur Einhaltung strenger Standards.
Medizinprodukte werden sowohl von der FDA als auch von der MDR auf der Grundlage des damit verbundenen Risikos in drei Klassen eingeteilt, für die jeweils spezifische gesetzliche Anforderungen gelten:
Medizinprodukte der Klasse I: Diese Geräte mit geringem Risiko stellen für die Benutzer nur eine minimale Gefahr dar und umfassen oft Artikel wie Verbände, Handschuhe und handgehaltene chirurgische Instrumente. Die regulatorischen Anforderungen sind relativ einfach und konzentrieren sich hauptsächlich auf die allgemeine Sicherheit und Qualität.
Medizinprodukte der Klasse II:Produkte mit mittlerem Risiko, wie z. B. Spritzen, Infusionspumpen und Diagnosegeräte, erfordern zusätzliche gesetzliche Kontrollen. Diese können eine besondere Kennzeichnung, Leistungsstandards und eine Überwachung nach dem Inverkehrbringen umfassen.
Medizinprodukte der Klasse III: Hochrisikoprodukte wie Herzschrittmacher, Defibrillatoren und Implantate erfordern die höchste Stufe der behördlichen Überwachung. Dazu gehören eine strenge Zulassung vor dem Inverkehrbringen, umfangreiche Tests und klinische Prüfungen zur Bestätigung der Sicherheit und Wirksamkeit.
Bei einem Diagnosegerät, das zur Erkennung von Infektionskrankheiten eingesetzt wird, muss beispielsweise jede einzelne Kunststoffkomponente verschiedenen Sterilisationsverfahren standhalten, ohne sich zu zersetzen oder schädliche Substanzen freizusetzen. Selbst geringfügige Verunreinigungen könnten die Genauigkeit des Geräts beeinträchtigen oder ein Risiko für die Patienten darstellen, was die Bedeutung dieser strengen gesetzlichen Standards unterstreicht. Die Einhaltung gesetzlicher Vorschriften ist beim medizinischen Spritzguss unerlässlich, da eine falsche Einstufung oder Nichteinhaltung zu Verzögerungen, höheren Kosten und einer längeren Markteinführungszeit führen kann.
2. Zertifizierungen: Gewährleistung von Qualität und Sicherheit
Die Zertifizierung ist ein Standard, der gewährleistet, dass die Produkte die Anforderungen der Branche erfüllen oder übertreffen. Zu den wichtigsten Zertifizierungen in der Medizinbranche gehören:
13485
ISO 13485: Diese Zertifizierung stellt sicher, dass ein Qualitätsmanagementsystem vorhanden ist, das die Konsistenz der Produktionschargen gewährleistet. Wenn Sie beispielsweise Infusionssysteme oder Beatmungsgeräte herstellen, ist die Zertifizierung nach ISO 13485 von entscheidender Bedeutung.
10933
ISO 10933: Für Teile, die direkt mit Körperflüssigkeiten oder Gewebe in Berührung kommen, gewährleistet die ISO 10993 die Biokompatibilität. Diese Zertifizierung ist für die Herstellung von Teilen wie Katheterspitzen oder Gehäusen für implantierbare Geräte unerlässlich, bei denen die Materialsicherheit direkte Auswirkungen auf die Gesundheit der Patienten hat.
14644
ISO 14644: Diese Reinraumzertifizierung ist entscheidend für die Vermeidung von Kontaminationen. Eine Reinraum-zertifizierte Einrichtung kann zum Beispiel sicher Komponenten für chirurgische Geräte herstellen, die eine sterile Umgebung erfordern, und so sicherstellen, dass sie den Krankenhaus- und Operationsstandards entsprechen.
14971
ISO 14971: Diese Zertifizierung stellt sicher, dass Risikomanagementverfahren vorhanden sind, die für Medizinprodukte von entscheidender Bedeutung sind. Sie ist beispielsweise bei der Herstellung von Teilen wie Infusionspumpen oder Herzschrittmachern unerlässlich, wo strenge Risikokontrollen zum Schutz der Patientensicherheit erforderlich sind.
3. Materialauswahl: Biokompatibilität und Langlebigkeit
Bei der Auswahl von Materialien für medizinische Anwendungen müssen auch andere Aspekte als die des Standardspritzgusses berücksichtigt werden. Beispiele hierfür sind:
• Polycarbonat (PC): Aufgrund seiner Festigkeit und Transparenz wird es häufig für Gehäuse von Geräten verwendet, die im Inneren sichtbar sein müssen, wie z. B. Blutanalysegeräte.
• Polyethylen (PE): PE ist für seine chemische Beständigkeit und Flexibilität bekannt und wird für Infusionsbeutel und Schläuche verwendet, die eine lange Haltbarkeit und geringe Feuchtigkeitsaufnahme gewährleisten.
• Polypropylen (PP): PP zeichnet sich durch eine hohe Schlagfestigkeit und Sterilisationsbeständigkeit aus und wird für Spritzen und medizinische Behälter verwendet, die eine langfristige Zuverlässigkeit bieten.
• Polystyrol (PS): PS wird häufig für Einweg-Laborgeräte verwendet und bietet Steifigkeit, Transparenz und einfache Sterilisation, wodurch es sich für Laboranwendungen eignet.
• Polyetheretherketon (PEEK): Aufgrund seiner Festigkeit, Sterilisationsbeständigkeit und Biokompatibilität wird es häufig für implantierbare Geräte verwendet.
• Thermoplastisches Elastomer (TPE): Aufgrund seiner Flexibilität eignet es sich für Griffe für chirurgische Instrumente, die sich weich anfühlen und einer wiederholten Sterilisation standhalten.
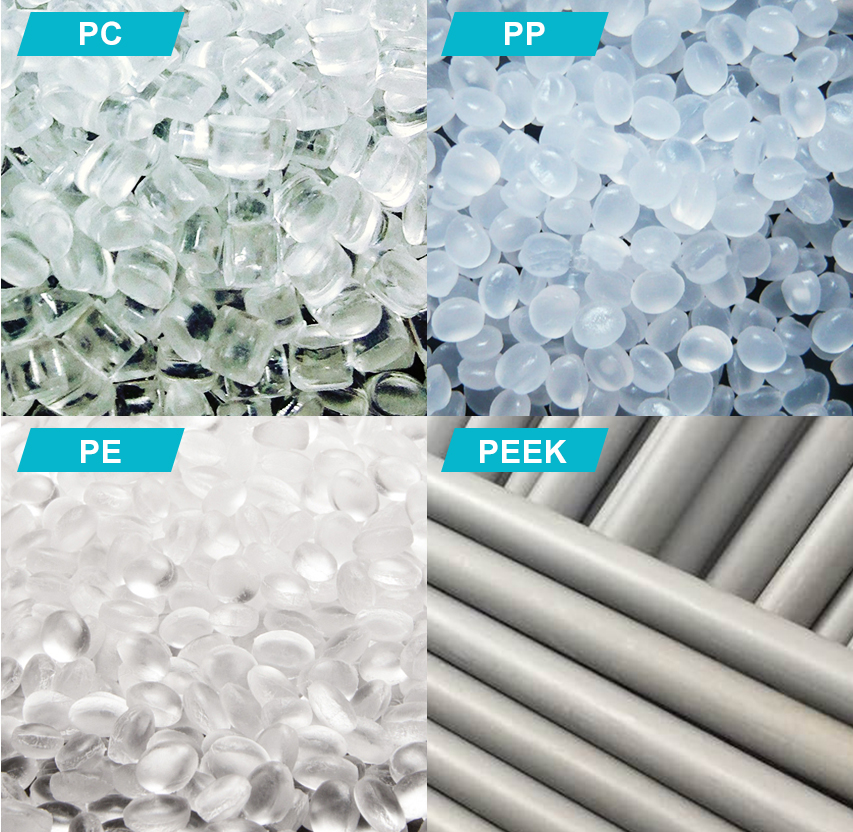
Jede Materialwahl bringt spezifische Kompromisse mit sich. So sind PE und PP zwar kostengünstig und chemisch beständig, haben aber möglicherweise nicht die erforderliche Festigkeit für Teile, die hohen Belastungen ausgesetzt sind. Daher hilft das Verständnis dieser Nuancen bei der Materialauswahl, um sowohl die Leistung als auch die Kosten zu optimieren. Klicken Sie hier, um mehr über die Auswahl von Materialien zu erfahren.
4. Vom Prototyping zur Produktion: Sicherstellung eines reibungslosen Übergangs
Der Übergang von Prototypen zur Serienfertigung ist nicht immer einfach. Während der Prototypenherstellung können Designs dünnere Wände oder komplexere Geometrien aufweisen, als sie mit Standard-Spritzgießverfahren im Maßstab leicht reproduziert werden können. Ein Prototyp mit scharfen Ecken kann beispielsweise im Vakuumgießverfahren hergestellt werden, erfordert aber eine Optimierung des Designs, wie z. B. das Hinzufügen von Radien und Entformungswinkeln, um ein effizientes Spritzgießen ohne Qualitätseinbußen zu ermöglichen.Bei der Skalierung kann ein erfahrener Spritzgusspartner mit Fachwissen und Fähigkeiten helfen, diese Designs für die Herstellbarkeit zu optimieren, ohne Kompromisse bei der Qualität einzugehen. Bei RPWORLD unterstützen wir unsere Kunden bei diesem entscheidenden Übergang, indem wir ihnen helfen, das Teiledesign zu optimieren, die am besten geeigneten Materialien und Nachbearbeitungsoptionen auszuwählen und vieles mehr, um eine effiziente und regelkonforme Produktion zu unterstützen.
Wie RPWORLD Injection Molding Ihre medizinische Entwicklung beschleunigt
Bei RPWORLD vereinen wir Werkstoffkompetenz, Fertigungsdienstleistungen aus einer Hand, eingehende DFM-Analysen und ISO-zertifizierte Prozesse, um Medizinprodukte schneller auf den Markt zu bringen. Unsere Dienstleistungen decken den gesamten Lebenszyklus ab - vom Prototyping bis zur Massenproduktion - und sind auf die individuellen Bedürfnisse jedes einzelnen Medizinprodukts zugeschnitten.
• Mehr als 20 Jahre Erfahrung im Spritzgießen von Medizinprodukten, vom Prototyping bis zur Endproduktion.
• Mold flow analysis und hausinterne Werkzeugkonstruktion und -herstellung.
• Eine große Auswahl an Nachbearbeitungsoptionen zur Perfektionierung Ihrer Teile.
Unsere Dienstleistungen im Bereich Spritzgießen umfassen:
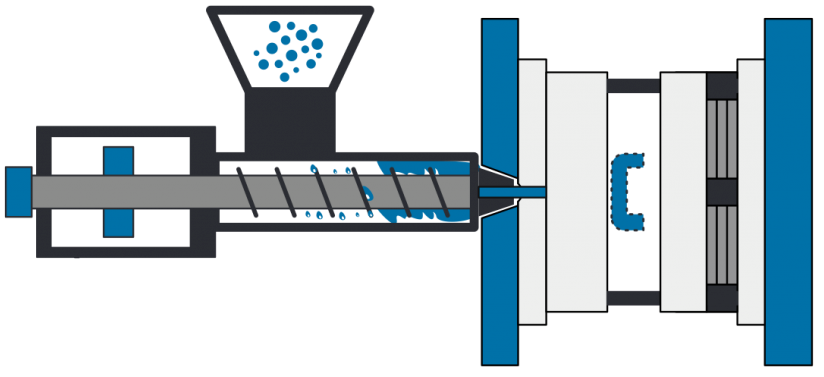
• DFM-Anleitung einschließlich Designoptimierung, Materialauswahl, Auswahl der Endbearbeitung und
• Hochmoderne Qualitätsprüfgeräte und
strenge Qualitätskontrollen, einschließlich Prozessüberwachung in Echtzeit, um Konsistenz zu gewährleisten.
Sind Sie bereit, Ihre Fertigung von Medizinprodukten zu verbessern? Setzen Sie sich noch heute mit
RPWORLD in Verbindung und erfahren Sie, wie wir Sie auf Ihrem Weg vom Konzept zur Realität unterstützen können.