Saviez-vous que le moulage par injection est en train de transformer l'industrie des dispositifs médicaux ? Ce processus avancé permet aux concepteurs de créer des produits de haute qualité et rentables, allant d'articles médicaux courants à des dispositifs hautement réglementés. À mesure que les produits franchissent les différentes étapes de leur développement, du prototypage initial à la production à grande échelle, ils doivent toujours répondre à des normes strictes en matière de conformité, de sécurité et de fonctionnalité. Cela permet de s'assurer que chaque dispositif médical est conforme aux exigences critiques de l'industrie à chaque étape.
Si vous envisagez de passer à l'étape suivante du moulage par injection médicale, cet article vous guidera à travers 4 considérations clés du moulage par injection médicale, de la compréhension des classifications des dispositifs et des réglementations à la sélection des matériaux appropriés et à la préparation de votre conception.
Principales considérations relatives au moulage par injection à des fins médicales
1. Conformité réglementaire : Respecter les normes correspondantes
Aux États-Unis, les directives de la Food and Drug Administration (FDA) imposent un suivi et une documentation rigoureux à chaque étape de la production afin de garantir la traçabilité de chaque composant. Dans le même temps, les normes du règlement sur les dispositifs médicaux (MDR) de l'UE mettent l'accent sur la sécurité des produits tout au long de leur cycle de vie, ce qui pousse les fabricants à respecter des normes strictes.
Les dispositifs médicaux sont répartis en trois catégories, tant par la FDA que par le MDR, en fonction du risque associé, chacune d'entre elles étant assortie d'exigences réglementaires spécifiques :
Dispositifs médicaux de classe I : Ces dispositifs à faible risque présentent des risques minimes pour les utilisateurs et comprennent souvent des articles tels que des bandages, des gants et des instruments chirurgicaux portatifs. Les exigences réglementaires sont relativement basiques et se concentrent principalement sur la sécurité générale et la qualité.
Dispositifs médicaux de classe II : Les dispositifs à risque modéré, tels que les seringues, les pompes à perfusion et le matériel de diagnostic, nécessitent des contrôles réglementaires supplémentaires. Il peut s'agir d'un étiquetage spécial, de normes de performance et d'une surveillance après la mise sur le marché.
Dispositifs médicaux de classe III : Les dispositifs à haut risque, notamment les stimulateurs cardiaques, les défibrillateurs et les implants, nécessitent le niveau le plus élevé de surveillance réglementaire. Cela inclut une approbation rigoureuse avant la mise sur le marché, des tests approfondis et des essais cliniques pour confirmer la sécurité et l'efficacité.
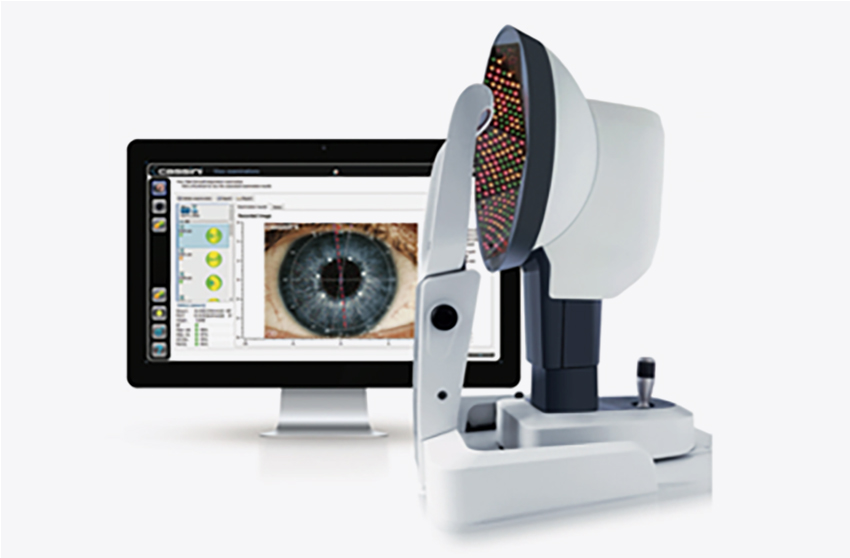
Par exemple, un dispositif de diagnostic utilisé pour détecter des maladies infectieuses nécessite que chaque composant en plastique résiste à divers processus de stérilisation sans se dégrader ni libérer de substances nocives. Une contamination, même mineure, pourrait compromettre la précision du dispositif ou présenter des risques pour les patients, ce qui souligne l'importance de ces normes réglementaires strictes. Garantir la conformité réglementaire est essentiel dans le domaine du moulage par injection médical, car une catégorisation incorrecte ou une non-conformité peut entraîner des retards, une augmentation des coûts et un allongement des délais de mise sur le marché.
2. Les certifications : Garantir la qualité et la sécurité
La certification est une norme qui garantit que les produits respectent ou dépassent les exigences de l'industrie. Les principales certifications dans l'industrie médicale sont les suivantes
13485
ISO 13485: cette certification garantit la mise en place d'un système de gestion de la qualité qui assure la cohérence des lots de production. Par exemple, si vous produisez des systèmes de perfusion ou des ventilateurs, la certification ISO 13485 est essentielle.
10933
ISO 10933: La norme ISO 10993 garantit la biocompatibilité des pièces qui entrent en contact direct avec des fluides ou des tissus corporels. Cette certification est essentielle pour la fabrication de pièces telles que les embouts de cathéters ou les boîtiers de dispositifs implantables, pour lesquels la sécurité des matériaux a un impact direct sur la santé des patients.
14644
ISO 14644: cette certification de salle blanche est essentielle pour prévenir la contamination. Une installation certifiée salle blanche, par exemple, peut produire en toute sécurité des composants de dispositifs chirurgicaux qui nécessitent un environnement stérile, garantissant qu'ils répondent aux normes hospitalières et chirurgicales.
14971
ISO 14971: Cette certification garantit la mise en place de processus de gestion des risques, ce qui est crucial pour les dispositifs médicaux. Elle est par exemple essentielle pour la fabrication de pièces telles que les pompes à perfusion ou les stimulateurs cardiaques, pour lesquels des contrôles rigoureux des risques sont nécessaires afin de protéger la sécurité des patients.
3. Sélection des matériaux : Biocompatibilité et durabilité
Le choix des matériaux pour les applications médicales implique des considérations qui vont au-delà du moulage par injection standard. Voici quelques exemples :
• Polycarbonate (PC) : En raison de sa résistance et de sa transparence, il est souvent utilisé pour loger des dispositifs nécessitant une visibilité interne, tels que les analyseurs de sang.
• Polyéthylène (PE) : Connu pour sa résistance aux produits chimiques et sa flexibilité, le PE est utilisé dans les poches et les tubes de perfusion, garantissant une durabilité et une faible absorption de l'humidité.
• Polypropylène (PP) : Grâce à sa forte résistance aux chocs et à sa stabilité à la stérilisation, le PP est utilisé dans les seringues et les conteneurs médicaux, offrant une fiabilité à long terme.
• Polystyrène (PS) : Largement utilisé pour les articles de laboratoire jetables, le PS offre rigidité, transparence et facilité de stérilisation, ce qui le rend adapté aux applications de laboratoire.
• Polyéther éther cétone (PEEK): Largement utilisé dans les dispositifs implantables en raison de sa résistance, de sa stabilité en stérilisation et de sa biocompatibilité.
• Élastomère thermoplastique (TPE) : Sa flexibilité le rend approprié pour les poignées d'instruments chirurgicaux doux au toucher qui résistent à des stérilisations répétées.
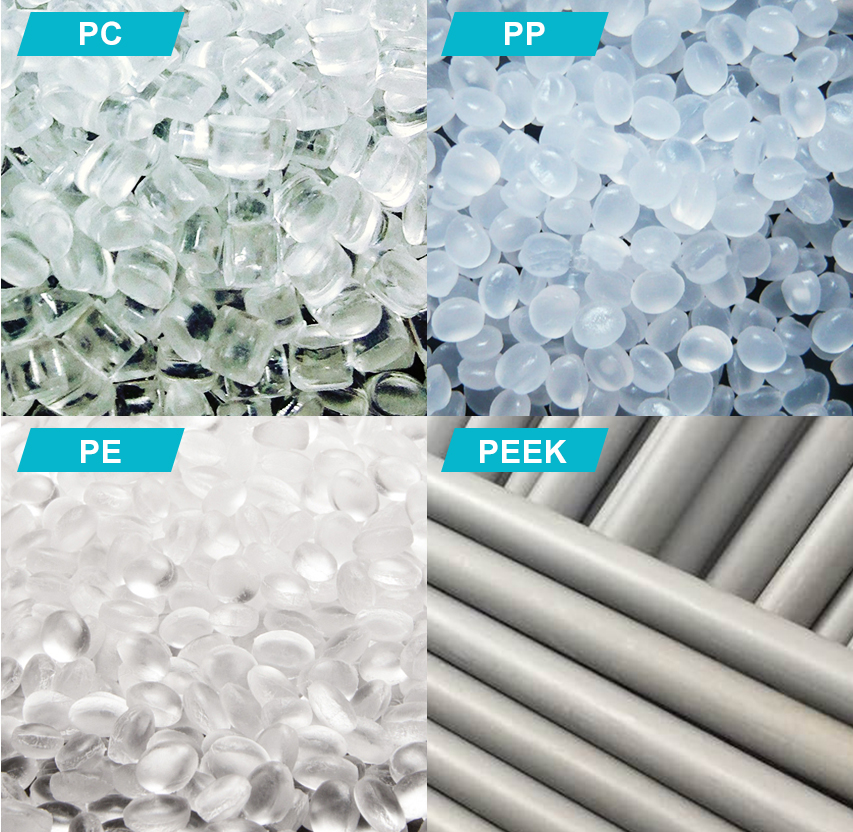
Chaque choix de matériau comporte des compromis spécifiques. Par exemple, si le PE et le PP sont rentables et résistants aux produits chimiques, ils peuvent ne pas avoir la solidité nécessaire pour les pièces exposées à des environnements très contraignants. Par conséquent, la compréhension de ces nuances facilite la sélection des matériaux, en optimisant à la fois les performances et les coûts. Cliquez ici pour découvrir d'autres choix de matériaux.
4. Du prototypage à la production : Assurer une transition en douceur
Le passage des prototypes à la production à grande échelle n'est pas toujours simple. Lors du prototypage, les conceptions peuvent présenter des parois plus fines ou des géométries plus complexes que les processus de moulage par injection standard peuvent facilement reproduire à l'échelle. Par exemple, un prototype avec des angles aigus peut être créé par le procédé de moulage sous vide, mais nécessite une optimisation de la conception, comme l'ajout de rayons et d'un angle de dépouille pour un moulage par injection efficace sans sacrifier la qualité.Lors de la mise à l'échelle, un partenaire expérimenté dans le domaine du moulage par injection, disposant de l'expertise et des capacités nécessaires, peut aider à optimiser ces conceptions pour qu'elles puissent être fabriquées sans compromettre la qualité. Chez RPWORLD, nous assistons nos clients dans cette transition cruciale, en les aidant à optimiser la conception des pièces, à sélectionner les matériaux les plus appropriés, les options de finition et bien d'autres choses encore, afin de favoriser une production efficace et conforme aux réglementations.
Comment le moulage par injection de RPWORLD accélère votre développement médical
Chez RPWORLD, nous intégrons l'expertise des matériaux, les services de fabrication à guichet unique, l'analyse DFM approfondie et les processus certifiés ISO pour accélérer la mise sur le marché des dispositifs médicaux. Nos services couvrent l'ensemble du cycle de vie, du prototypage à la production de masse, et s'adaptent aux besoins spécifiques de chaque dispositif médical.
• Plus de 20 ans d'expérience dans le moulage par injection de dispositifs médicaux, du prototypage à la production finale.
• Analyse de l'écoulement du moule et conception et fabrication d'outils en interne.
• Une grande variété d'options de post-traitement pour perfectionner vos pièces.
Nos services de moulage par injection comprennent
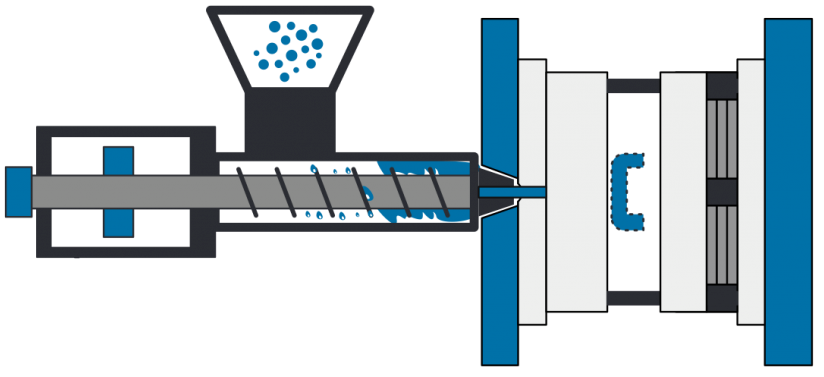
• Conseils en matière de conception pour la fabrication (DFM) y compris l'optimisation de la conception, la sélection des matériaux, la sélection des finitions et plus encore, afin d'éviter les retouches coûteuses et de gagner du temps jusqu'à 80 %.
• Un équipement d'inspection cohérence. de la qualité à la pointe de la technologie et un contrôle de la qualité rigoureux, y compris un suivi des processus en temps réel pour garantir la
Vous êtes prêt à améliorer la fabrication de vos dispositifs médicaux ? Contactez
RPWORLD dès aujourd'hui et découvrez comment nous pouvons vous aider à passer du concept à la réalité.