ПРОЕКТНЫЙ ФОН
Клиент, один из ведущих в мире производителей автоматизационных машин, выбрал RPWORLD для предоставления квалифицированных прототипов и решений малых серий для ежемесячного заказа 40 единиц. У них была новая инструментальная машина на стадии ИС и О, и ключевой компонент, сборка крыльчатки, вышла из строя, что привело к задержке всего процесса разработки продукта.
1. Как выбрать наиболее подходящее производственное решение для удовлетворения потребностей клиента?
2. Как добиться плотного прилегания в сборке крыльчатки?
3. Как обеспечить долговременную работу сборки крыльчатки под водой?
4. Как обеспечить высокое качество и как можно скорее запустить продукт в производство?
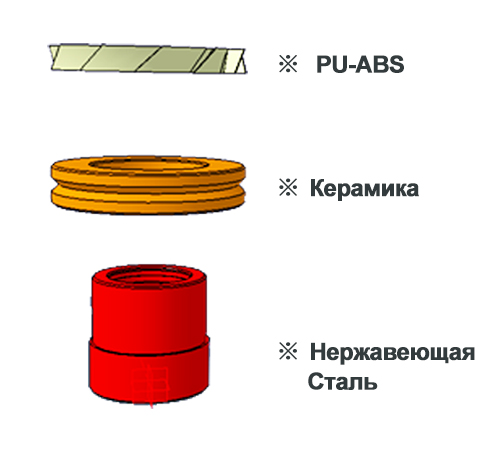
1. Повторное тестирование неудачной сборки крыльчатки
Чтобы найти первопричину производства прототипа, мы снова изготовили прототипы с тем же производственным процессом и провели повторное тестирование неудачной сборки крыльчатки.
● Изготовить крыльчатку методом ЧПУ и склеить вместе обычным клеем, специальным клеем и т. д.
● Изготовить крыльчатку методом ЧПУ, провести поверхностную обработку металлической и керметной части, чтобы сделать их шероховатыми, затем склеить 3 части вместе.
После нескольких тестов выяснилось, что метод ЧПУ и склеивание не соответствуют требованиям сборки.
2. Пробный новый производственный процесс
Учитывая проб и ошибок сборки крыльчатки, RPWORLD наконец решил попробовать вакуумное литье для проведения эксперимента.
● Изготовить мастер-модель методом 3D-печати.
● Изготовить раму для формы, смешать жидкий материал и поместить в вакуумную машину в первый раз.
● Разместить сборку крыльчатки в раму для формы и установить место разъема формы.
● Разместить сборку крыльчатки в раму для формы и установить место разъема формы.
● Поставить в печь для постоянного температурного отверждения на 3-4 часа.
● Разъединить форму и, наконец, выполнить послепроцессинг для завершения образца.
Образец был отправлен клиенту для подводных испытаний. И нам сообщили, что образец, изготовленный вакуумным литьем, прошел тест на долговременную работу под водой.
● Время производства сократилось на 50%;
● Стоимость производства составила всего 20%-30% от стоимости традиционных решений для изготовления инструмента.
● Долгосрочный партнер по разработке продукции.
● Клиенты наслаждались беспроблемным тестированием прототипов и сэкономили много времени и средств на научно-исследовательские и конструкторские работы.
● Вся производство, послепроизводственная обработка и предварительная сборка выполнялись единым поставщиком, RPWORLD, что значительно снижало риски проекта.
● Тесное общение и профессиональное координация обеспечивали высокое качество и соблюдение графика запуска.
В итоге, RPWORLD стал системным поставщиком сборки лопаточных аппаратов, и станок для изготовления инструментов успешно продавался по всему миру. RPWORLD также стал долгосрочным и стратегическим партнером клиента.